#
Electrolytic Processes
# Introduction
Various markets and sectors across the global economy are exploring the role of electrolysis for hydrogen production. As the project pipeline develops, investments in relevant technologies and infrastructure are currently in the billions of U.S. dollars (USD). Companies are considering how adopting hydrogen as a low- or zero-carbon energy carrier or fuel will impact costs, reliability, and flexibility of operations within their value chain. From bulk/long-duration energy storage in the electricity grid, to hydrogen-derived AECs, electrolytic processes have the potential to support many decarbonization pathways. The short-term outlook is mostly focused on increasing electrolyzer capacities and improving economies of scale to drive down costs. The long-term outlook is more complex as the role of electrolyzers in producing hydrogen in an integrated energy system are not fully defined or understood. The objective of the Electrolytic Processes TSC is to evaluate technologies and inform technical and strategic directions for advancing broader deployment and adoption across the energy economy.
The field of electrolysis includes both mature and developing technologies. Commercial units have been deployed for over 100 years and new technologies aim to reduce costs, boost efficiencies, and increase operational flexibility. The total capacity of electrolyzers shipped from manufacturers to customers in 2020 is estimated to be almost 30% higher than in 2019—reaching 200 megawatts (MW). Another 17 GW are currently planned, while BNEF expects 2021 will see more than double the deployment of 2020. This surge is driven in part by nine countries and the European Union which have recently released roadmaps outlining the development of a hydrogen economy to address climate and economic-related goals. The European Union alone has established plans to install at least 40 GW of electrolyzers by 2030 (BNEF 2021).
Despite the recent increase in demand, cost effectiveness and operational flexibility of electrolyzer systems are two remaining unknowns as sectors and industries look to deploy low- and zero-carbon energy. As noted earlier, hydrogen production by electrolysis comprises less than two percent of global production today, with nearly all of the remaining 98% supplied by natural gas reforming or coal gasification processes (IEA 2019b). Various organizations have established electrolyzer production cost targets ranging from approximately $0.50 to $2 USD/kg (~$4 to $17 USD/MMBtu). In the summer of 2021, the U.S. Department of Energy announced a Hydrogen Shot challenge to reach $1 per kilogram of clean hydrogen in one decade. Preliminary analysis from the LCRI Integrated Energy System Analysis TSC suggests today's electrolysis production costs range from $3.50 to 5.50 USD/kg (~$31 to 48 USD/MMBtu).[1] The difference in today's values versus targets may lead to competition from steam-methane reforming (SMR) or other commercially available methods that could integrate CCS in support of low-carbon energy production. The LCRI estimates hydrogen production costs using SMR with CCS (at 90% CO2 capture) is currently on the order of $1.40 USD/kg ($12 USD/MMBtu).[2]
The Electrolytic Processes TSC has identified three focus areas for LRCI R&D activities to address critical aspects of cost, operations, and integration of electrolyzer systems. These focus areas are Technology and System Integration, Advanced Technology Development, and Process Modeling and Analysis.
The TSC arrived at these focus areas through evaluation of the current global market for electrolyzer technologies and the anticipated growth of the market over the next 30 years as many parts of the energy economy establish pathways to achieve deep carbon reductions. There are relatively few manufacturers of electrolyzers currently capable of delivery at large commercial scale (>10 MW in capacity), and with recent project announcements and the numerous sectors vying for low-carbon energy carrier solutions, demand for electrolyzer technologies could soon outpace current manufacturing capabilities. Manufacturers of the two commercially available electrolyzer technology types, alkaline and proton exchange membrane (PEM), are already responding to the need to speed up capital cost reductions. Many capital cost reductions will likely be achieved by economies of scale as the influx of new orders allows manufacturers to invest in cost-saving production capabilities and strengthen their supply chains. However, a significant amount of hydrogen production costs are associated with the price of electricity (up to 75% in some cases) and capacity factor of the electrolyzer (NREL 2021). More research is needed to better understand and characterize systems-level integration and operational perspectives and how these technologies might need to interact and respond to both electricity supply and hydrogen demand volatility. This TSC plans to develop resources to guide deployment of commercial technologies at larger scale and share lessons learned and perspectives from global efforts. Resources may take the form of technology evaluation reports, engineering and operations guidelines, results from studies conducted through the LCRI or collaborations (for example, lab-scale, pilot and/or demonstration-scale testing), and energy and material balance assessments.
Novel technologies, such as solid oxide electrolysis (SOEC), anion exchange membrane (AEM), and other technologies (for example, membrane-less and hybrid units), require significant development, demonstration, and durability testing before commercial deployment can occur. By taking a long-term perspective to economy-wide decarbonization, the possibility of these technologies scaling up over the next 10 years seems reasonable. If successfully developed, these novel technologies could potentially lead to significantly reduced capital and operating costs with improved system integration capabilities compared to technologies deployed today. This TSC plans to develop evaluation protocols to inform decision makers on methods to compare technology options in consideration of new alternatives becoming available in the future. Upon completing a thorough analysis of the current advanced technology landscape, the TSC intends to identify and evaluate the necessary steps to achieve commercial deployment and communicate likely pilot- and demonstration-scale requirements. This analysis will include an assessment of opportunities for the LCRI to lead pilot or demonstration testing of technologies.
Unfortunately, there is not a one-size-fits-all approach for evaluating the technoeconomics of hydrogen production by electrolysis as there are several factors to consider. In addition to specific characteristics associated with technology type, durability, capacity factor impacts, energy source, geographic location, proximity to end users, and balance of plant (BOP) systems each play a role when comparing technology options. To address the evolution of electrolyzer technologies and advancement of new technologies/systems, this TSC plans to develop and manage analysis tools to provide insight into cost and performance trends and projections.
# Key Research Questions
Over the course of the LCRI, the TSC intends to address the following research questions.
Which electrolysis technologies are currently or readily available to various sectors?
What are the relative competitive advantages and limitations of each technology (for example, the size of commercial entities, current product offerings, plans for future expansions in offerings and manufacturing)?
What are the capital and operational costs and what are the main factors driving these values?
Which systems or components have room for cost reductions at scale?
What are the key operating parameters?
What are the anticipated timelines for mass/large market production?
What are current vendor offerings and what are they developing for future products?
What electrolysis technologies are emerging as promising alternatives in the near term?
What advantage(s) do they bring?
What factor(s) are holding their development and/or deployment back?
What is a timeline to commercialization?
What supply chain sensitivities could affect the hydrogen production space?
Are current or emerging technologies developing alternative lower-cost catalysts or critical materials?
Is there a system in place for recycling and recovery of critical materials or system components?
Are there standard safety technology operations from a product and system perspective, including consideration for integration and siting aspects?
What are additional BOP requirements (for example, electronics, cooling, water treatment, power controls) and how do they contribute to the cost of hydrogen?
What is the expected electrolysis system lifetime and how do operational decision factors affect that lifetime?
What are the environmental aspects (for example, water demand and utilization, emissions) of each technology option?
How do we understand system performance flexibility (for example, efficiency, capacity factor) when considering capital cost optimization versus operations load following to maximize the value proposition of hydrogen energy production?
Can (or when might) hydrogen from electrolysis be cost competitive with hydrogen production from other clean hydrogen production alternatives such as SMR with CCS?
How might electrolyzer systems support integrated energy activities (for example, grid services, consumer demand, excess electricity generation utilization)?
What are the system performance characteristics and integration requirements that would better inform siting of electrolysis technologies with existing grid assets (for example, where thermal inputs can increase system efficiency)?
How might stakeholders need to be informed to make important decisions for incorporating electrolysis technologies into business plans?
What are the tradeoffs for understanding capital cost of the system, electricity cost, and capacity factor on the cost of hydrogen production?
What are the regulatory factors that will impact the deployment of electrolysis now and in the future?
What transition factors are critical to driving the need for hydrogen production using electrolysis (for example, integration with the electric grid and clean energy production, timelines for transitioning various sectors/industries)? How will these factors play out over the next 30 years as decision are made to achieve 2050 goals?
How might regional/geographic drivers influence the transition towards more hydrogen production adoption?
How will the costs of transporting and storing hydrogen influence deployment of hydrogen production?
# Research Effort
The Electrolytic Processes TSC has organized the research plan around three focus areas to address the current and projected landscape for electrolysis technologies and systems. These three areas are summarized in Figure 18.
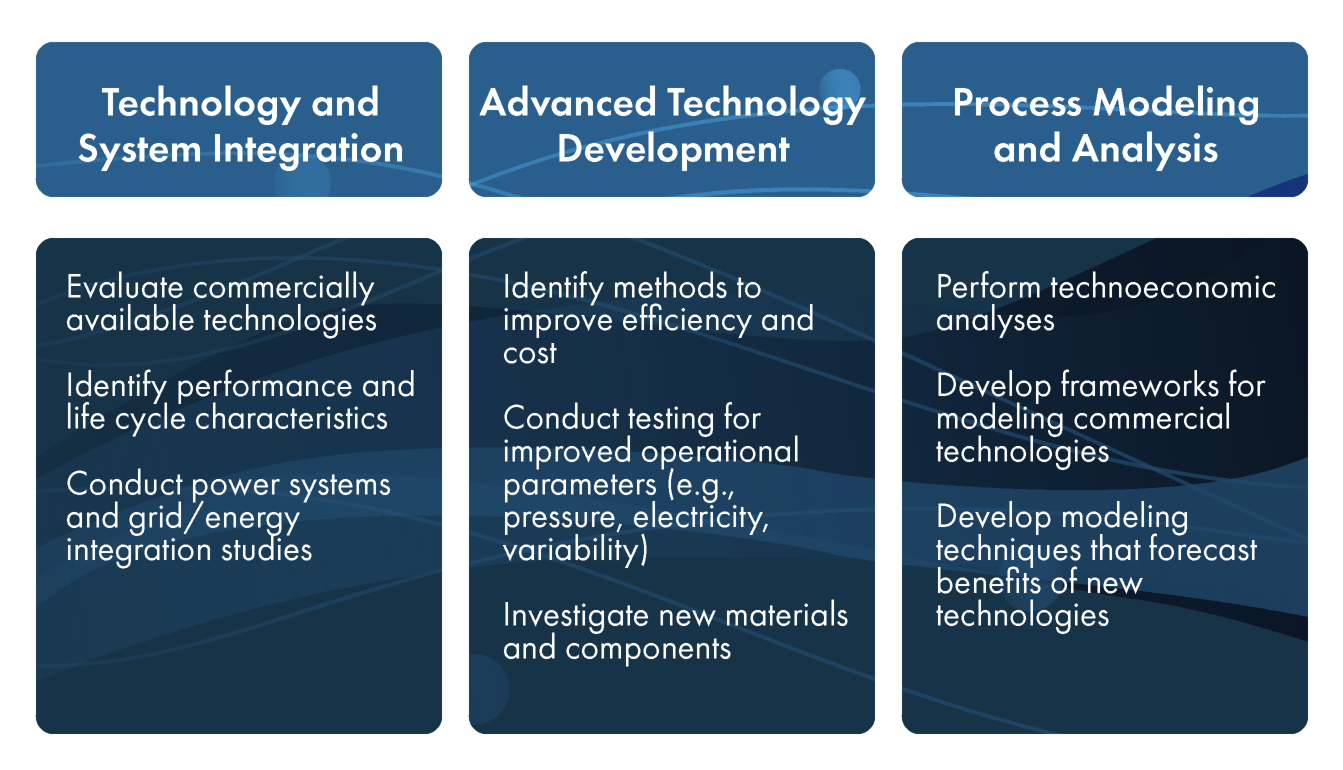
Electrolysis has the potential to serve as a mechanism for low- or zero-carbon energy production for many sectors of the economy. To address the variety of options, better characterize the functions electrolysis could serve, and ensure coverage of the possible uses of electrolysis within the LCRI, a value chain approach to the TSC research plan is proposed. A description of this value chain approach is presented in Figure 19.
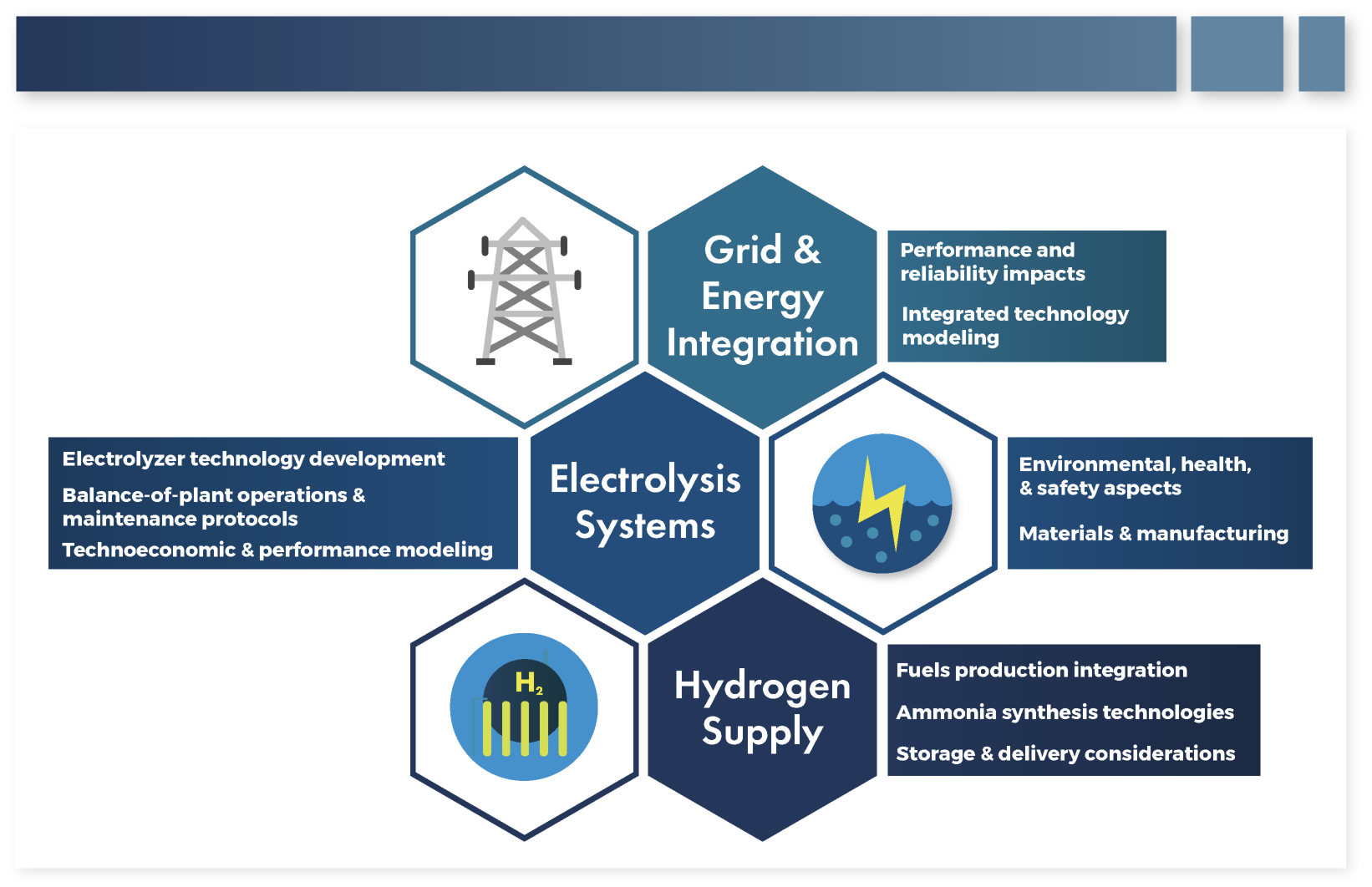
# Research Goals
The overall research objective for this TSC is to understand and advance the hydrogen production industry in accordance with the goals of the LCRI. The Electrolytic Processes TSC aims to collect comparable information across the hydrogen production space for current and emerging technologies and develop methodologies to inform decision making on technology development and portfolio choices (for example, energy production, end use applications, geographic constraints, storage, and delivery capabilities).
A summary of the proposed research effort and associated goals is provided below.
# Goal 1: Support large-scale technology and system integration
Strategy 1: Understand current state-of-the-art and develop gap analysis for future technology deployment
- Action: Evaluate commercial technologies. Create a state-of-technology report, conduct interviews with technology vendors, and investigate BOP operations and maintenance protocols.
Strategy 2: Characterize operations and maintenance, environmental aspects, and benefits and limitations of the technology
- Action: Identify performance and life cycle characteristics.
Strategy 3: Characterize current status and projections for larger-scale deployment impacts on BOP systems (for example, power electronics, water treatment, cooling, hydrogen storage/compression)
- Action: Evaluate BOP systems and assess protocols (operations, maintenance, safety, and environmental).
Strategy 4: Understand the risks, challenges, limitations, and benefits of system integration
Action: Conduct power systems and grid integration studies to evaluate performance and reliability impacts.
Action: Conduct integrated technology analyses (for example, electric grid, direct renewable, nuclear). Leverage pilot or demonstration-scale activities where possible.
Strategy 5: Working across sectors/industries, support safe deployment of electrolysis technologies
- Action: Develop safety considerations for operation of systems.
Strategy 6: Characterize water consumption and other impacts
- Action: Develop water utilization and treatment analysis tools and establish metrics.
# Goal 2: Identify and lead efforts to accelerate advanced technology development
Strategy 1: Reduce the cost of hydrogen by improving operations understanding and their effect on production cost
Action: Identify methods or technologies to improve efficiency and cost.
Action: Conduct testing for improved operational characteristics (for example, pressure, electricity variability).
Strategy 2: Understand the effects of critical supply chain factors on the cost of hydrogen
- Action: Investigate the potential and opportunity of deploying new materials or processing methods.
# Goal 3: Develop process modeling and analysis resources
Strategy 1: Make informed and economically sound decisions
- Action: Develop technoeconomic analyses tools and resources for commercial technologies and placeholders for advanced technologies.
Strategy 2: Understand realistic scenarios for, and implications of, hydrogen generation, including economics, storage, operating requirements
- Action: Develop frameworks and tools for modeling commercial technologies.
Strategy 3: Identify the potential roles of advanced technologies in future applications
- Action: Develop modeling techniques that estimate benefits of new technologies.
Strategy 4: Improve the state-of-the-art operation efficiency and durability of electrolysis cells and develop deployment strategies for energy resource considerations
- Action: Create technology analysis tools, including flow field modeling and energy resource modeling.
# Anticipated Role of the LCRI in Technology Development
The TSC routinely evaluates the landscape of commercial and developing technologies relevant to the research goals. The TSC has organized technologies by anticipated role of the LCRI in technology development (see Figure 20). The TSC seeks to balance many considerations when choosing the anticipated level of activity. These considerations include projected deployment timeframe, level of effort, focus, and investment of other organizations/initiatives with similar goals, potential role in supporting various industries/sectors in decarbonization strategies, and amount of relevant information available to conduct thorough analyses, among others. Over the course of the initiative, the TSC intends to update these positions based on research results from ongoing TSC activities and energy-economy modeling results produced by the Integrated Energy System Analysis TSC.
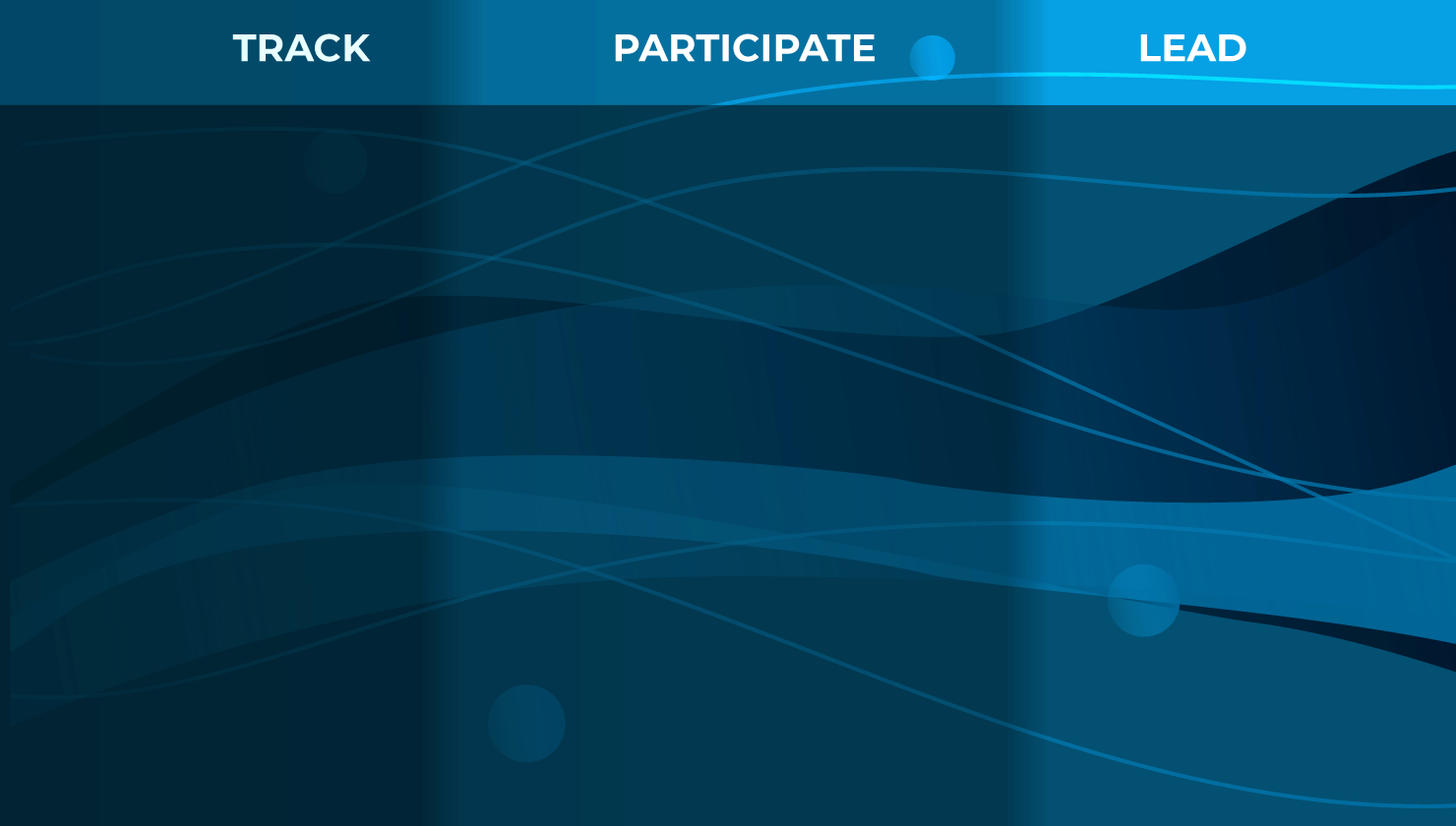
Please select "+" pushpins to see more details.
# Joint Areas of Research with Other Technical Subcommittees
The list below outlines areas where joint research with, and integration of, activities from other TSCs will be necessary.
Hydrogen production and storage safety and environmental aspects.
Production of synthetic fuels from electrolytic hydrogen, including:
Ammonia;
Methanation;
Fischer-Tropsch fuels; and
Methanol.
Systems that need or can leverage the by-product oxygen created by water electrolysis.
Hydrogen storage technologies.
Integration with power generation and other high-volume end-uses.
Hydrogen blending with the natural gas infrastructure.