# Hard-to-Decarbonize Applications
There are two broad reasons an application might be characterized as hard to decarbonize. It may be that solutions exist to decarbonize the application but for some reason the solution is expensive to implement (for example, technology nascency, expensive materials, expensive to retrofit). For other applications it may be that a solution to decarbonize the application has not been fully demonstrated or, in some cases, does not exist. Because of their outsized role in emissions and the relatively broad applicability of solutions, technologies to decarbonize the electricity grid and land-based passenger transportation sector have largely already been identified and are being scaled, though a notable exception to decarbonizing electricity is discussed later in this section. However, long haul transport—whether by road, sea, or air—and numerous industrial processes generally lack proven solutions for decarbonization or the solutions that exist are expensive relative to the existing, carbon emitting options. Therefore, these economic sectors make up the majority of the applications identified as having significant abatement costs (that is, greater than $600/ton CO2e) or that are not abatable with current technologies (see Figure 9).
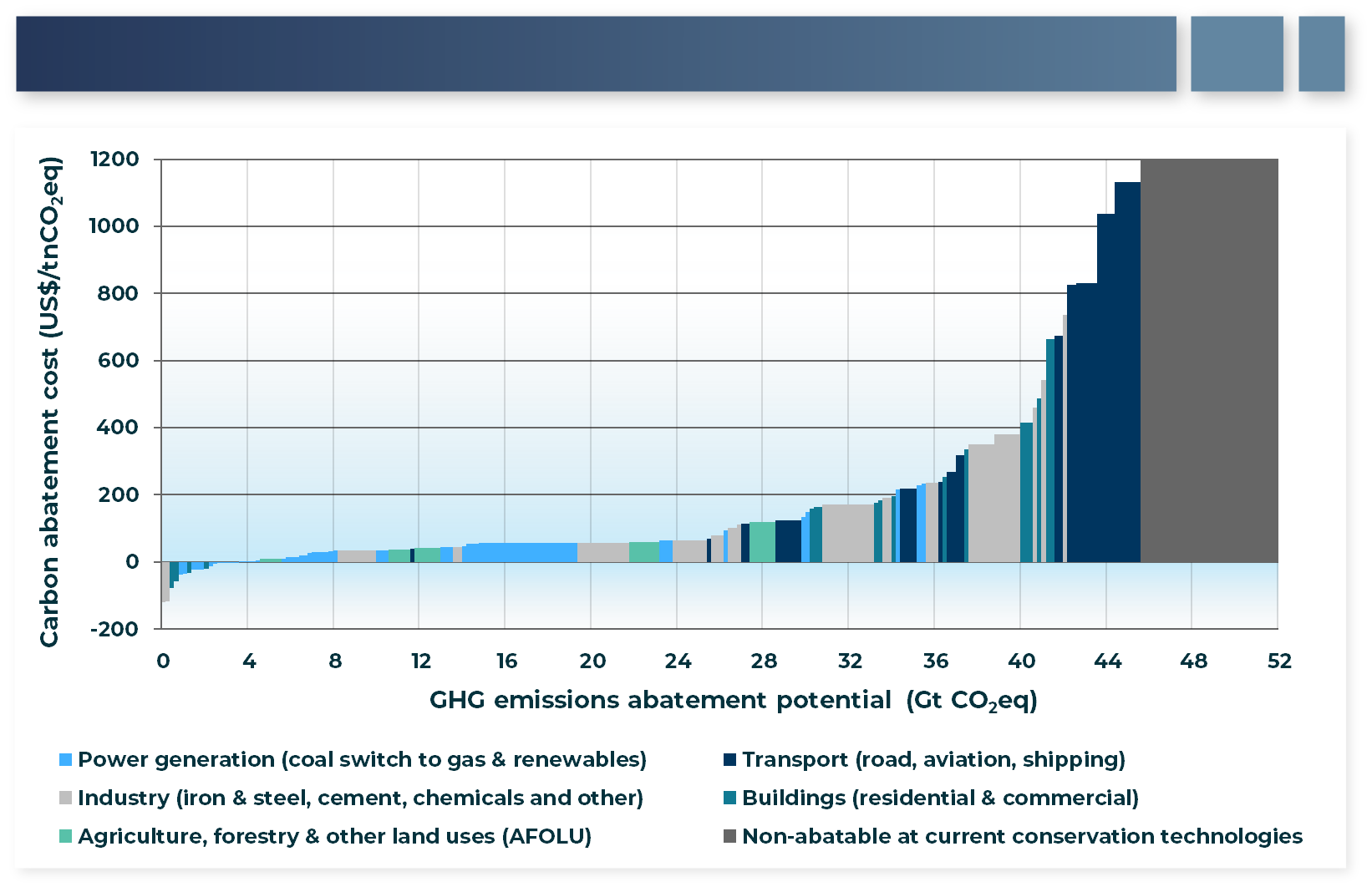
# Long-Duration Energy Storage
As the amount of variable renewable energy increases on the electricity grid there is a need to balance the daily, weekly, and seasonal variation of the electricity production of these resources. This variability presents a two-fold challenge. The first is that to fully decarbonize the electricity grid there is a need for emission-free solutions to fill in these various gaps in intermittent renewable generation. The second challenge is that deploying enough capacity of these resources to meet energy demand for a large portion of the year will necessarily result in over-production from these resources in many other parts of the year. Figure 10 shows an extreme example of this on the Eastern Interconnect of the U.S. with 40% of electricity demand being met by solar and 60% from offshore wind (generally representative of a zero-emission scenario).
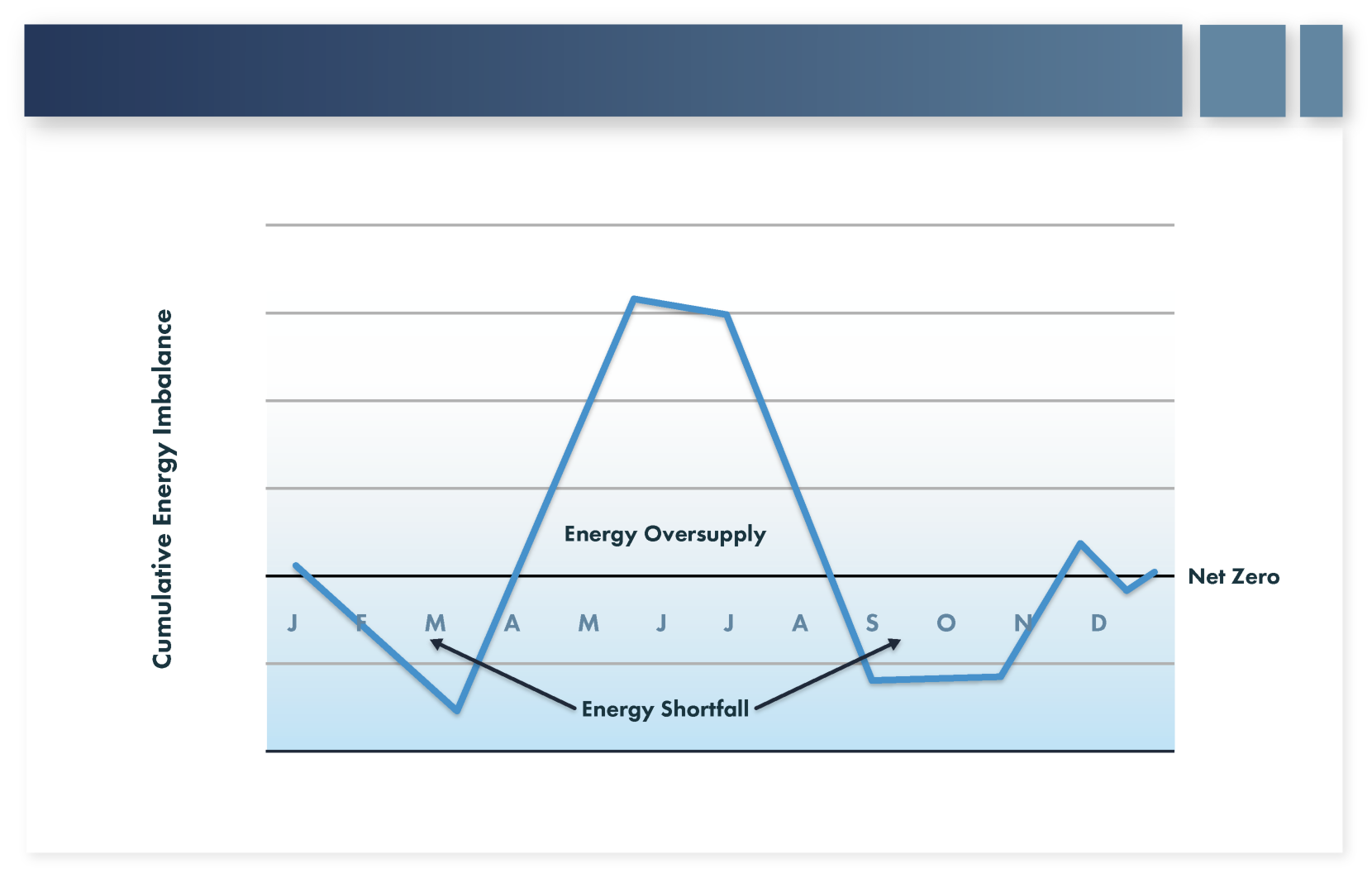
There is currently significant momentum around the deployment of lithium-ion (Li-ion) batteries as a solution to these challenges. Although there is not a technical limit on the duration of storage that Li-ion batteries could service, currently they are thought to be best suited for relatively short durations (<8 hours) due to their high marginal costs (that is, each additional kWh of energy storage requires purchasing an additional, relatively expensive, battery cell). There are also challenges with energy leakage (self-discharge) if energy is to be stored in the batteries for more than a few days. Other storage solutions such as pumped storage hydropower (PSH), compressed air energy storage (CAES), or thermal energy storage (TES) are potential technologies suitable for longer durations of energy storage, but are still likely to be limited to ~24-48 hours of duration because of the requirement for increasing size as the desired storage duration grows.
Although the combination of these aforementioned solutions is likely to fill many of the gaps in production on a variable renewables-heavy grid, there may still be a need to fill in seasonal gaps for energy production from variable renewables. Critical events may only occur once per year—or even less frequently—from causes that could range from extreme weather (for example, polar vortexes, hurricanes) to volcanic eruptions and earthquakes to wildfires. Although these may be relatively infrequent occurrences, they typically result in disruptions that may last for weeks or more while creating situations in which energy availability is critical. Therefore, there may be a need to identify and develop carbon-free energy sources capable of being stored in volumes sufficient to service large energy needs—potentially up to the entirety of daily load for a period of weeks—without degradation while stored over a period of months to years.
# Industrial Sector
In 2018, the industrial sector accounted for approximately 39% of global, energy related GHG emissions. There are several reasons decarbonizing the industrial sector is particularly challenging:
Industrial processes often require high-temperature heat ranging from 700°C to over 1,600°C. This heat is typically produced by fossil fuels and their replacement with electricity or hydrogen will require significant change in production processes and/or development of alternative furnace designs.
Industrial processes are frequently tightly integrated, meaning that a change to one step in the process may require modifications to other steps. For example, if an ethylene steam cracking furnace were electrified there would be a reduction in the excess heat provided by combustion—which is currently used to make high-pressure steam for compressors and turbines further into the production process.
Energy use in the industrial sector is, generally, already highly optimized and efficient. Therefore, unlike the building and passenger transport sectors, increased electrification is less likely to result in significant operational cost savings. In addition, capital cost for electrified equipment is largely the same as, or even higher than, that of conventional equipment.
Many industrial products, such as steel and cement, are commodities for which cost is the primary consideration in purchasing decisions. Decarbonization options that increase the cost of production could create a market disadvantage (absent a willingness to pay more for a decarbonized commodity).
A significant amount of the emissions from the industrial sector does not come from energy use, but rather the processing of a feedstock (for example, limestone in cement, natural gas in ammonia). These emissions can be reduced only by changing the feedstock or adding carbon capture to the process.
Industrial equipment lifetimes are often on the order of 20-40 years, which inhibits the pace of market turnover or transformation.
An additional challenge is that decarbonizing industrial processes may require a move away from a standardized process to one that is appropriate for the locality in which the good is produced, which could disadvantage some producers or locations in the production of commodities. Some of the factors that may advantage certain locations, and by association local firms, over others include:
Access to low-cost, reliable, zero-carbon electricity
Access to sustainably produced biomass
Availability of CCS capacity
Broadly, this reinforces the fact that there is no single pathway for decarbonizing an industrial process and that a portfolio of solutions will likely be needed to fully decarbonize the industrial sector. The challenges in decarbonizing the industrial sector and the optionality required are reflected through the discussion of potential decarbonization pathways for two significant industrial processes—cement and steel production—in Appendix B.
Used with permission from Goldman Sachs. The views of EPRI and GTI do not represent the views of Goldman Sachs, nor are the views expressed in this document endorsed by Goldman Sachs. ↩︎